The product development process is incomplete without prototyping. The designer needs to validate the manufacturability, functionality and economic value of physical products. The prototyping processes are vital links between concept validation and manufacturing. The prototyping processes use scaled-down versions, minimalist or unrefined versions of the final product. The designer uses these inexpensive models to identify design shortcomings, potential usability defects, and cost of production and analyze the impact of the desired consumer product on productivity.
For several years, designers and product development managers have developed several technologies to improve turnaround times for creating functional prototypes. It has given birth to different rapid prototyping processes and technologies. These technologies continue to evolve with time, with industrial design companies selecting a method that is the best fit for their business operations.
Which rapid prototyping technologies can upcoming innovators, established companies, and individual designers use to bring their ideas into reality? What factors should product developers evaluate before selecting an affordable prototyping technique? Let us explore the different rapid prototyping techniques, discuss the benefits of each and provide an easy-to-follow prototyping guide.
Do you have a physical product or mobile app idea you want to launch?
What is rapid prototyping?
Rapid prototyping refers to the quick production of consumer product models. The model can be a standalone part or an assembly that mimics the desired end product. The prototype should showcase the working mechanisms of the designed component and incorporate the critical features of the product. Rapid prototyping converts 3D CAD models into physical product models. The fabrication of these prototypes is possible using additive manufacturing processes, while others are achievable through subtractive manufacturing.
Prototyping processes are critical for the testing phase of the product development cycle. The designer can effectively evaluate the early market success of the product based on its unique features. Rapid prototyping processes are not one-off activities. The product development team iterates initial product designs based on the test results and available feedback. The team experiments with several manufacturing techniques and materials.
The first step begins with creating a computer-aided design (CAD) model. It is either a 2-dimensional or 3-dimensional product design. Afterward, the designer transfers the CAD model to a rapid prototyping machine which interprets the prototype design and generates fabrication codes. In some cases, the designer develops the manufacturing codes manually. Rapid prototyping done using an additive manufacturing process joins several layers of material to create a product that has the exact shape of the designed product. In a subtractive manufacturing process, the prototyping equipment strips off layers of material from a solid piece to replicate the shape and size of the CAD design.
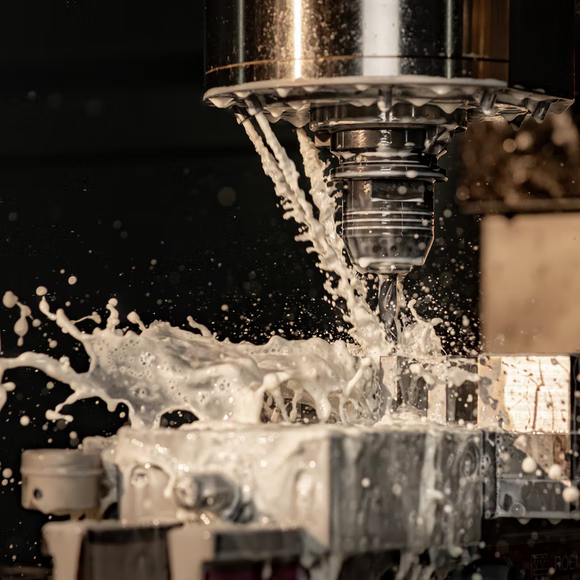
CNC machining is one of the subtractive prototyping processes
Benefits of rapid prototyping processes
Businesses are competing to retain a sizeable share of the consumer markets. Companies and innovators must deliver finished products within short timelines and adhere to the highest quality standards. In the age of invention design, product developers must collect feedback from their target markets before releasing products. It means that the industrial design company should invest in rapid prototyping. It allows them to test consumer products fast and cheaply. What benefits can businesses gain by streamlining their rapid prototyping processes?
Quicker exploration of concepts
A typical invention design process involves generating, developing and testing different product concepts. The innovator identifies one or more viable solutions and begins refining them to satisfy particular user needs. Prototyping processes provide economical means for designers to explore and develop product concepts faster. They shorten the product development lifecycle and ensure the designer visualizes the final product using low-fidelity and high-fidelity prototypes.
Easy communication of complex ideas
Some solutions to predominant consumer problems may appear complex to stakeholders and consumers. They may not understand the working mechanisms of a product or an assembly and could shun the product. However, by developing a functional prototype, the designer or industrial design company can communicate complex ideas effectively. The customer or stakeholder sees how the final product looks and follows through with the problem-solving process. That way, the innovator receives impressive buy-in from potential clients and investors.
Improves iterative design processes
Rapid prototyping processes enable product developers to test and validate unconventional mechanisms and ideas. Some of these ideas work at the first trial, while others require readjustment before they become functional. A prototype helps the product designer to identify potential usability challenges. They then capitalize on the design defects and shortcomings to steadily improve the functionality and reliability of consumer products.
Saving costs by identifying design flaws early
An industrial design company must comprehensively validate that the final product is viable for manufacturing and devoid of flaws before mass production. The overall cost of manufacturing increases if the company implements corrective measures on already manufactured parts due to defects. Prototyping processes enable the company to decide on surface finishing methods, assembly techniques, product appearance, manufacturing materials and quality assurance measures. Identifying and eliminating product defects earlier saves companies several thousands of dollars once full-scale production begins.
Application areas of rapid prototyping processes
As mentioned earlier, rapid prototyping is a work in progress. It has sustained several years of development and improvement. The technology was popular among automotive production facilities. Over time, the technology found its way to the aerospace sector and manufacturing. Currently, the technology is established in several sectors dealing with consumer products. Any industry dealing with mass production relies upon rapid prototyping to streamline the product development process and expand revenues through deliberate and accidental invention design.
Rapid prototyping applies to proof-of-concept processes to introduce new, disruptive or innovative consumer products. It means companies can develop prototyping processes for fashion products, medical devices, packaging solutions, original equipment manufacturer (OEM) parts or engineering prototypes. In each situation, the product developer creates a prototype design to validate testing and manufacturing processes.
Do you have a physical product or mobile app idea you want to launch?
Rapid prototyping techniques
Several prototyping techniques exist in the market. Each prototyping method has desirable benefits. The choice of the prototyping method depends on several variables. But first, let us explore how each technology works.
Stereolithography (SLA)
3D printing technology builds on the early success of the SLA technique. The prototyping process relies on ultraviolet (UV) lights to solidify the printing liquid. The intensity and concentration of the UV lights are controlled using a computer system. The printing fluid is sensitive to a concentrated light. When the photosensitive fluid interacts with the UV light, it solidifies. It creates a layer-by-layer model or product.
Stereolithography is an additive technique. The UV laser traces out the consumer product or part as it appears on the CAD model. The layer by layer part fabrication ensures that the surface finish is smooth. Product developers can create components with complex geometries. The prototyping technique uses photopolymer resins which solidify immediately after exposure to UV light.
Photopolymer resins are weaker than specialized engineering-grade resins. Therefore, prototypes created using SLA are suitable for limited functionality tests.
Selective Laser Sintering (SLS)
Designers seeking to create prototypes from plastic or metallic material can utilize this rapid prototyping technique. The additive manufacturing method creates layer-by-layer prototypes. It also has a laser head that heats and heals the powdered prototyping materials. The SLS machine contains a powder bed where the manufacturing materials lie. During this process, the laser traces the part design on the bed containing powdered fabrication material.
As UV light strikes the powder, it begins fusing to form a solid. It creates a thin layer of solidified material. Once the layer is fully-fused, a fresh powder supply is placed on the bed. The sintering material begins until the finished product meets the design specifications.
The selective sintering process utilizes high-strength materials and enables industrial design companies to create tough prototypes. The process is suitable for products with complex geometries, although the surface finish is usually rough.
Injection molding
The prototyping process uses thermoplastic material for the creation of product molds. Traditionally, injection molds were fabricated from steel materials. However, modern injection molding equipment relies on an aluminum-based mold. The prototyping machine injects heated thermoplastic resins into the mold, which has the shape of the desired end product.
Injection molding allows innovators and designers to develop strong prototypes with superior surface finishes. The end product features smooth edges, making the technology a preferable alternative for companies dealing with plastic products.
Injection molding uses standard thermoplastic materials or liquid silicone rubber. Prototypes made from these products have suitable engineering strengths and do not limit functionality tests. The only disadvantage of this prototyping process is the high cost of tooling. Injection molding requires more than one additive or subtractive manufacturing process. For instance, most companies create molds using computerized numerical control (CNC) machining.
Fused deposition modeling (FDM)/ Material jetting
An inexpensive 3D printing technology. The printing head ejects heated thermoplastic material under pressure. The printing material (filament) passes through a nozzle where it is heated before deposition on the fabrication bed. The molten material is applied layer-by-layer, forming a solidified prototype as designed on the CAD software.
Fused deposition modeling enables innovators to create functional prototypes from different materials. These materials melt before extrusion and solidify in layers to create a prototype. Common materials used for material jetting prototyping processes include; ABS, polycarbonate, or a combination of both.
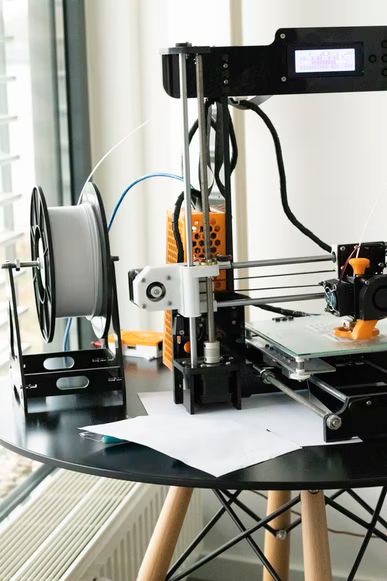
3D printing is among the popular prototyping processes that uses advanced thermoplastic material
The prototyping process is cheap and suitable for creating prototypes having different strengths. The surface finish depends on the smoothness of the initial layer.
Direct metal laser sintering(DMLS)
It is an effective rapid prototyping process for developing metallic prototypes using powdered material. It enables product developers to create functional prototypes and several end-use products. A layer of powdered metal material is applied to the bed of the prototyping machine. The DMLS equipment contains a laser head that traces the cross-section of the end product on the surface of powdered metal. When the laser strikes the metal surface, it welds the atomized powder, forming strong solid models.
Once welding of a layer is complete, a fresh supply of powder material is placed on the fabrication bed. The laser process repeats until the shape and size of the 3D model are achieved. DMLS utilizes several metal alloys. That way, product development teams fabricate highly detailed prototypes for full-scale functional testing. Apart from creating strong and durable prototypes, the technique enables innovators to incorporate complex designs into the prototype. The designer can include internal details like passages, keys, or joints that are difficult to create using conventional manufacturing practices like casting. The mechanical and structural properties of the prototype are similar to those of the desired end product. DMLS prototypes have a rough surface finish. They are more costly than other prototyping processes and demand additional post-fabrication treatment.
Polyjet
It is a rapid prototyping process that uses a specialized printing head to spray photopolymer resins on the printing surface of 3D printing devices. The printer has an ultraviolet light source that strikes the sprayed polymer layers and cures them instantly. The direction and shape of the laser mimic the CAD model in shape and size. Polyjet printing uses very thin layers of materials, enabling product development teams to refine the quality and resolution of prototypes and end products. Usually, the printing process uses a gel matrix to support the thin layers of material. The matrix is removable once the prototyping process is complete.
Binder jetting
A unique prototyping process enables product developers to create prototypes from two different materials. The binder jetting equipment has a powder bed where the innovator places sufficient quantities of powdered materials. It has a nozzle that sprays fine droplets of binding fluid onto the powder bed. In the process, the two materials fuse, forming a solid prototype in the shape and size of the 3D/2D CAD model.
The binder compacts each layer before supplying a fresh blend of powder. After the process is complete, the prototype is subjected to post-treatment. It is placed in an oven where it heats, curing the surface, burning off the binding material and fusing the powdered layers into one solid product.
Digital Light Processing
The rapid prototyping process is similar to SLA. The only variation is the use of conventional light to bind and cure the polymer resins. The printing process uses gel-based support structures to hold the fragile layers together during the fabrication process. Prototypes made using digital light processing require additional treatment after formation to enhance their strength for functional testing. It enables designers to create cheap prototypes and improve the surface finish of prototypes.
CNC Machining
It is a popular subtractive manufacturing technique that is crucial for rapid prototyping. The process begins by clamping a metallic or non-metallic fabrication material on the CNC machine. The CNC tool is either a lathe or mill, depending on the machining preferences. CNC machines strip off materials from the solid surface until the desired prototype is formed. CNC machining facilitates the creation of products with superior surface finishes.
CNC machining depends on computerized systems to control the tooling and operating speed of the equipment.
Choosing a suitable rapid prototyping process for your business
At one point in the product development process, companies must create prototype designs and proceed to fabrication and testing. One may assume that choosing a rapid prototyping technique is a pick-and-go activity. The reality is different. The product manager grapples with a multitude of challenges. What are the budgetary constraints? Which desirable and functionality features are to be tested? How fast is the turnaround time, and what resources are available?
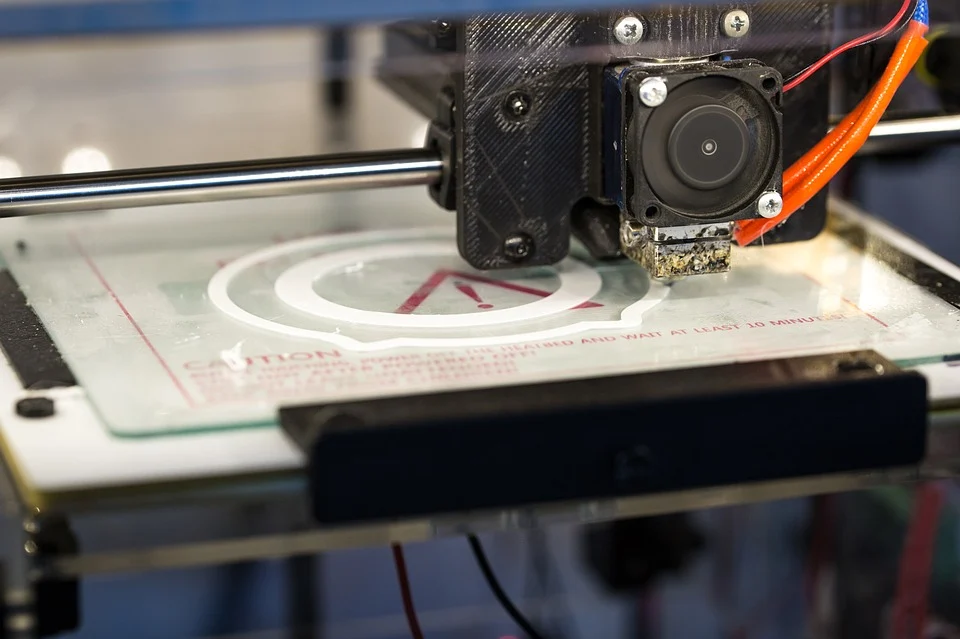
Layer by layer material deposition to create functional prototypes
The choice of the prototyping technique should reflect the company’s aspirations and offer tangible value. There is no need to spend a ton of money conceptualizing ideas only to choose a prototyping process that is technically and economically untenable.
There are a few factors that a product developer needs to evaluate before settling on a rapid prototyping process. Consider:
Design software
Before prototype fabrication, designers create hyper-realistic CAD models using different design software. The native CAD models have diverse file formats. The designer converts design files into a format compatible with the rapid prototyping device. Some devices can interpret more than one file format, while others read specific file formats. Ensure that the design and prototyping software and file formats are compatible. The file conversion process should retain product design features to limit errors and production defects.
Verification of measurement units
When designing products, engineers use different standards of measurements. Perhaps the desired size of the final product is several meters long. When prototyping, the industrial design company scales down the design model. Before beginning the rapid prototyping process, verify the units of measurement.
The unique prototype features
The function of a prototype is to test the functionality, form and quality of physical products. In some designs, designers are interested in specific details like tolerances, allowances, surface finish or offsets. Choose a rapid prototyping process that facilitates the replication of the finer details.
Quality over cost
Why does the cost of rapid prototyping matter? After all, the company wants a shorter turnaround time. When choosing a prototyping process, it is critical to set clear testing objectives. The rapid prototyping technique chosen could be cheap but limits the functionality of a product. On the contrary, a costly process could enable the product development team to visualize detailed design requirements.
Final remarks
Rapid prototyping remains pivotal in the product development process. A prototype enables the design team to actualize product concepts. A functional prototype offers sufficient insights to guide the team toward full-scale production. Several rapid prototyping processes exist in the market. Each method offers unique advantages to the innovator. The product design and development team needs to evaluate the prototyping needs before settling on a technique. Rapid prototyping processes continue to evolve. As an innovator, you must look out for cheap prototyping processes with high returns on investment.